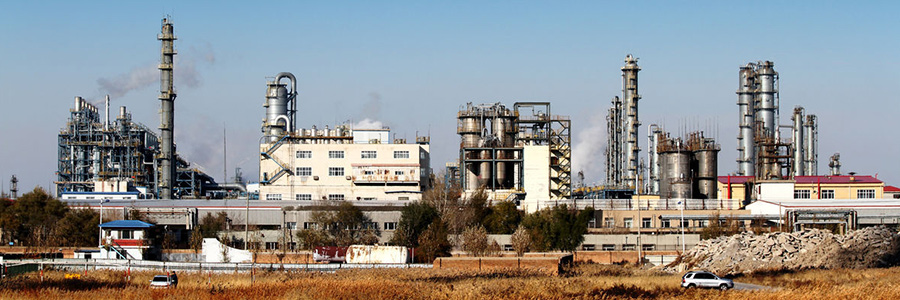
天津石化乙烯裂解炉低氮燃烧器国产化改造获得全面成功
在正常工况下,天津石化烯烃部全部6台裂解炉连续运行6个月,氮氧化物排放量稳稳地保持在56.3-80.6毫克/立方米之间,取得阶段性成果之后,通过后续优化攻关,日前,在烧焦工况下,裂解炉氮氧化物排放量检测数值控制在53.6-79.8毫克/立方米以内,标志着天津石化成为国内应用国产低氮燃烧器控制氮氧化物排放技术、取得全流程减排改造成功的第一家,这也是该公司绿色发展取得了又一重要成果。
近年来,天津石化公司积极响应国家环保治污、节能减排、循环经济的号召,认真履行央企社会责任,不断加大环保和节能的投入和改造。为适应《石油化工工业污染物排放标准》要求,满足国家从2017年7月1日裂解炉烟气中氮氧化物含量控制在100毫克/立方米以下的环保规定,早在去年9月份,天津石化烯烃部就利用设备大检修之机,提早进入氮氧化物减排改造工程的实施。其中,1号裂解炉是实施首批改造的设备之一,主要通过采用国产加工制造技术,完成了新型低氮燃烧器改造,实现氮氧化物合规排放。
此次改造采用燃料分级燃烧和分级配风以及烟气循环的低氮氧化物燃烧先进技术,主要包括对烧嘴砖、风箱、风量调节器、燃气枪、长明灯等裂解炉底部燃烧器组件进行改造,以及对烧嘴砖及托砖板、引射燃气喷枪、箱体、风量调节器等侧壁燃烧器组件进行的改造。通过降低燃烧器的火焰峰值温度实现低氮燃烧,从而有效降低烟气中氮氧化物的排放量,达到减少空气污染源的目的。
由于裂解炉工作温度较普通加热炉高,高达1200度左右,在此情况下,氮氧化物极易生成,其排放量控制难度较大。不仅当时国内应用国产低氮燃烧器,使氮氧化物排放量稳定控制在90毫克/立方米以内的,没有完全成功的先例,而且选用国外技术也没有完全成功的案例。
为保证项目早日实现稳定运行,按要求通过环保验收,1号炉实施改造后,烯烃部认真做好燃烧器的调试检测工作。他们安排专人与设备制造厂家在现场边调试边检测,持续跟踪检测氮氧化物、一氧化碳排放量等参数。密切关注裂解炉主要操作参数的变化,搜集数据,分析各主要参数的变化趋势。
与此同时,操作人员不断调整裂解炉底烧和侧烧的供热比例,并对燃烧器的喷头规格、开孔尺寸、开孔方向、加工和安装精度进行了调整,实现了改造项目的持续优化。不仅如此,他们还多次召开专题会议,进行技术讨论,逐步摸索出该炉裂解不同形态原料的适宜操作方式和供热比例,使裂解炉氮氧化物排放日趋稳定,直至实现了长效平稳运行。
今年2月份,天津市环保局对1号裂解炉应用低氮燃烧器控制氮氧化物排放项目进行严格检测,检测工况的裂解原料为轻烃,生产负荷分别达到14吨、15吨,每个负荷下检测两组数据,每组数据时间间隔为一小时,最终顺利通过环保验收。
6月份,烯烃部完成了对全部6台裂解炉低氮燃烧器改造,经天津市环保检测验收,所有裂解炉在正常运行工况下,氮氧化物排放指标达到56.3-80.6毫克/立方米,低于100毫克/立方米的国家标准,较改造之前的平均检测值160毫克/立方米,足足减少了50%。在取得阶段性改造成果的基础上,该部继续对烧焦工况排放控制进行了优化攻关,并取得了成功。