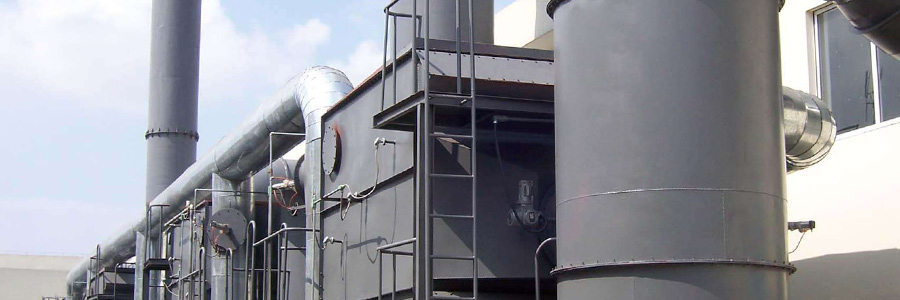
当前工业余热回收利用的现状与技术
余热资源普遍存在,特别在钢铁、化工、石油、建材、轻工和食品等行业的生产过程中,都存在丰富的余热资源,所以充分利用余热资源是企业节能的主要内容之一。
余热利用的潜力很大,在当前节约能源中占重要地位。余热资源按其来源不同可划分为六类:1 高温烟气的余热;2 高温产品和炉渣的余热;3 冷却介质的余热;4 可燃废气、废液和废料的余热;5 废汽、废水余热;6 化学反应余热。
从经济性出发,需要结合工艺生产,进行系统整体的设计布置,综合利用能量,以提高余热利用系统的效率。
根据余热利用过程中,能量的传递或转换特点,可将国内目前工业余热技术,分为热交换技术、热功转换技术、余热制冷制热技术。
热交换技术
热交换技术是最直接、效率较高的经济方法,在不改变余热能量形式下,通过换热设备将余热能量,直接传递给自身工艺的耗能过程,降低一次能源消耗。主要利用方式有间壁式换热、余热锅炉、蓄热式热交换、热管的换热等。
热功转换技术
利用热功转换技术,可提高余热的品位,是工业余热另一重要技术。
按照工质分类可分为,以水为工质的蒸汽透平发电,和以低沸点工质的有机工质发电。
目前主要以水为工质,以余热锅炉+蒸汽透平或者膨胀机,所组成的低温汽轮机发电。
制冷制热技术
与传统压缩式制冷机组相比,吸收式、吸附式制冷系统,可利用廉价能源,低品位热能避免电耗,具有显著节电效果,得到广泛应用。
吸收式余热制冷机组,制冷效率高,适用于大规模热量回收。而吸附式制冷系统结构简单、无噪音、无污染,可用于颠簸震荡场合,更适合小热量回收,或用于冷热电联产系统。
热泵以消耗一部分(电能、机械能、高温热能)作为补偿,通过制冷机热力循环,把低温余热源“泵送”到高温热媒,热泵常被用于,回收略高于(30~60℃)废热,达到节能降耗目的。
进行余热回收原则是
- 对于排出高温烟气的各种热设备,其余热应优先由本设备或本系统加以利用。如预热助燃空气、预热燃料等,以提高本设备热效率,降低燃料消耗。
- 在余热余能无法回收用于加热设备本身,或用后仍有部分可回收时,应利用来生产蒸汽或热水,以及生产动力等。
- 要根据余热的种类、排出情况、介质温度、数量及利用的可能性,进行企业综合热效率及经济可行性分析,决定设置余热回收利用设备的类型及规模。
- 应对必须回收余热的冷凝水,高低温液体,固态高温物体,可燃物和具有余压的气体、液体等的温度、数量和范围,制定利用具体管理标准。
热管技术在余热回收应用的原理和方法
超导热管的原理
热管技术的应用国际上是在20世纪60年代,主要是应用于太空飞行器,今天我们利用超导热管技术服务于余热回收和热能利用,为企业、社会取得显着的经济效益和社会效益。
超导热管是依靠其内部工质在一个抽成一定的真空的封闭壳体中循环相变而传递热量的装置,其工作原理是:当热量自高温热源传入热管时,处于热管加热段内的工质随即被激活,吸热汽化变成蒸汽(汽化段),蒸汽瞬间流向热管另一端(传输段),到达另一端时遇冷放出潜热后凝结成液体(冷凝段),冷凝液体经传输段回流到汽化段,循环相变而实现热量传递。
超导热管的超强导热系数是一般金属的万倍左右,换热效率高达98%以上,是任何一种普通热交换器无法达到的。
热管技术的重要特点
与常规换热技术相比,热管技术之所以能不断受到工程界欢迎,是因其具有如下的重要特点。
- 热管换热设备较常规设备更安全、可靠,可长期连续运行。这一特点对连续性生产的工程,如化工、冶金、动力等部门具有特别重要的意义。常规换热设备一般都是间壁换热,冷热流体分别在器壁的两侧流过,如管壁或器壁有泄漏,则将造成停产损失。由热管组成的换热设备,则是二次间壁换热,即热流要通过热管的蒸发段管壁和冷凝段管壁才能传到冷流体,而热管一般不可能在蒸发段和冷凝段同时被破坏,所以大大增强了设备运行的可行性。
- 热管管壁的温度有可调性。热管管壁的温度可以调节,这在低温余热回收或热交换中是相当重要的,因为可以通过适当的热流交换把热管管壁温度调整在低温流体的露点以上,从而防止露点腐蚀,保证设备的长期运行。这在电站锅炉尾部的空气预热方面应用得特别成功,设置在锅炉尾部的热管空气预热器,由于能调整管壁温度不仅能防止烟气结露,而且也避免了烟灰在管壁上的黏结,保证锅炉长期运行,并提高了锅炉效率。
- 冷、热段结构和位置布置灵活。由热管组成的换热设备的受热部分和放热部分结构设计和位置布置非常灵活,可适应于各种复杂的场合。由于结构紧凑占地空间小,因此特别适合于工程改造及地面空间狭小和设备拥挤的场合,且维修工作量小。热管换热设备效率高,节能效果显著。
热管换热器
利用热管导热能力强、传热量大的特点,以多根热管作为中间传热元件,实现冷、热流体之间换热的设备叫热管换热器。按照热流体的状态,热管换热器可分为气-气式、气-液式、气-汽式。从热管换热器结构型式来看,热管换热器又可分为整体式、分离式、回转式和组合式。
1、整体式热管换热器热管换热器的典型结构如图所示。热管平行交错排列在换热器内,中间用隔板将每根热管分隔成两部分,一部分与热流体通道相连,为热管的蒸发段;另一部分与冷流体通道相连,为冷凝段。冷、热流体均在热管外部横向流过,通过热管轴向传输热量,将热从热流体传给冷流体。
根据热管换热器的传热特点,它最适宜于气-气之间的换热。因为它在冷、热段均可加翅片来扩展传热面积,大大提高以管基为基准的传热系数。它也可作为气-液换热器,此时只需在烟气侧加翅片,以增强传热,但是,对液-液之间的换热,热管换热器并不能显示出它的优点。
下图为气-液热管换热器示意图,它的一个重要特点是气侧热管管壁破坏时,水侧的水不会漏入气侧,增加了设备使用的可靠性。
下图为热管余热锅炉的两种结构型式。冷侧一般均为承压的锅筒(或与锅筒系统相连通)。目前热管余热锅炉产生的蒸汽压力可达12MPa。进入余热锅炉的烟气温度最高可达1100℃。热管余热锅炉的最大特点是结构紧凑,体积小,安全可靠。与一般的烟管式余热锅炉相比,其质量仅为烟管式余热锅炉的1/3-1/5,外形尺寸只为烟管式余热锅炉的1/2-1/3。烟气通过余热锅炉压力损失一般为20~60Pa,故引风机的电耗也很小。热管元件的破损,不影响蒸汽系统的循环,无需为此停机检修。
2、分离式热管换热器分离式热管换热器如图所示,其蒸发段和冷凝段相互分开,两者这前通过蒸汽上升管和冷凝液下降管连接成一个循环回路。其循环动力为下降管系统(包括冷凝段)与上升管系统(包括蒸发段)中工作介质的密度差,即不需要外加动力,但存在着一个最小高度差Hmin,冷凝段与蒸发段的高度差必须大于Hmin。分离式热管换热器拥有一些常规换热器不具备的特性:根据现场实际情况,可灵活地布置蒸发段和冷凝段;一种热流体可同时加热两种不同的冷流体(如空气和煤气如图所示)安全而可靠;管排内的蒸气温度可以调整。如图所示,在分离式热管换热器中,改变蒸汽上升管和冷凝液下降管的连接次序,可以调整管排内的蒸气温度,这样可以避免高温侧因管内温度高而造成的压力过高的安全性问题和因低温侧温度过低带来的露点腐蚀问题。
3、回转式热管换热器该类换热器有两个显著的优点:一是借助转动的离心力来实现工作液体循环,同时转动促使气流的搅动,增强传热,这结含尘较多的气体更为有效。二是这类换热器兼有送风机的功能。但由于增添了转动机构使结构复杂化,另外还增加了动力消耗。回转热管换热器可分为离心式、轴流式和涡流式。
4、组合式热管换热器整体式热管换热器均由同一类型的热管所组成。而组合式热管换热器则是根据换热器中所处的温度段不同,而选用最适宜在该温度区内工作的热管。
5、热管换热器与其他型式的换热器的比较热管换热器与其他型式的换热器相比,有以下特点:
- 传热性能高。尤其对气-气热管换热器,更能显示出它的优点。
- 传热平均温差大。冷、热流体的通道布置方便,流向可以布置成单纯的逆流形式。
- 结构紧凑。除上述特点可使换热器做的紧凑外,每根热管的传热能力也大,可以用较少热管数目保证热量的传递。
- 布置灵活。热管可以作为通用的传热元件,对于传热量要求不同的换热器,可以用改变热管根数的方法进行任意组合。
- 工作安全可靠。每根热管是独立的传热元件,即使其中一根发生故障,也不影响整个换热器的正常工作。在检修时,可以单独进行更换。
标签: 燃烧技术