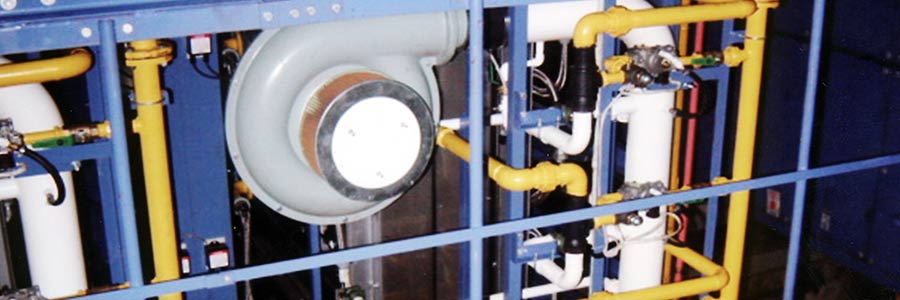
电磁搅拌技术应用广泛
随着对增加产量和在最小投资前提下降低操作成本的要求不断增加,铝工业对电磁搅拌技术的兴趣也在不断增加。本文的目的是简要介绍电磁搅拌技术(Al-EMS),并介绍其对提高生产率、收得率、改善操作条件的效果,以及在新领域的应用。自1947年开始对铝工业和钢铁工业提供各种电磁搅拌器。目前已向熔铝炉、静置炉、连铸机和钢包炉提供了1100多套电磁搅拌器。第一台铝电磁搅拌器(Al-EMS)在1969年由ASEA公司安装于一台单室熔铝炉上。以后,即使电磁搅拌技术被认为需要高投资成本,电磁搅拌器的数量也在不断增加。因此电磁搅拌器主要安装于大于70t的熔铝炉上。但电磁搅拌技术经过不断改进,即使在小炉子上。目前已经能够与其他搅拌方式相竞争,现在全世界有150多套铝电磁搅拌器,其中日本的数量最多,因为电磁搅拌技术在日本被认为是铝熔炼过程的标准技术。
电磁搅拌技术(Al-EMS)是一项已被证实和广为采用的对熔铝炉和静置炉中铝液进行有效搅拌的技术。目前已在全世界安装了150多台铝电磁搅拌器。能够缩短熔炼时间、增加产量、减少炉渣的形成、加快合金熔化和成分均匀、大幅度降低生产成本,设备投资回收期在很多情况下短于1年。铝熔池的有效搅拌能够增加冶金反应速度、改善传热和传质过程,是提高生产效率、改善铸造质量和降低操作成本的关键因素。电磁搅拌技术是对熔铝炉和静置炉中铝液进行搅拌的有效技术,并广为接受。通过改善传热和传质过程以及反应动力学,电磁搅拌技术能够缩短熔炼时间、减少炉渣形成,大幅降低操作成本。
电磁搅拌线圈是线圈为水冷式,安装于炉子底部或侧部,线圈与炉体之间没有直接的物理接触。可以采用通常的炉衬厚度,为了保证磁场进入熔池,必须在线圈前方的炉壳上安装奥氏体不锈钢窗。线圈采用低频行波磁场,磁场穿透炉壳和炉衬对熔池实现搅拌,其作用机理类似于线性电机。Al-EMS可以安装于新建炉子上,也可安装于改建炉子上,对于后者通常采用侧装式,圆形熔铝炉的侧装式系统包括一个或多个线圈、一个变频器、一个变压器、一个水冷站和控制系统,搅拌器可以采用本身的控制系统或连接于炉子控制系统进行操作,可以采用共用的电源和冷却水系统以尽量节省空间和降低成本。
电磁搅拌与人工搅拌和气体搅拌的比较,有14炉采用电磁搅拌和少量的气体搅拌,有16炉仅采用气体搅拌,采用电磁搅拌后,炉渣量由2.53%减少到2.15%,给出了圆形反射炉上的试验结果。有14炉采用电磁搅拌,17炉采用人工搅拌。试验过程中,废铝的加入比例从0到100%,其余为重熔铝锭,在使用电磁搅拌时平均废铝加入比例为80%,没有电磁搅拌时废铝比例为71%,在这种情况下,炉渣量从2.5%降到1.9%。采用人工搅拌时产生较多的炉渣主要有两个原因,一是在不进行搅拌时熔池表面温度过高,导致较高的氧化速率,另一个是在人工搅拌时熔池表面产生强烈的湍流,使大量铝熔滴卷入渣层内。
在有无电磁搅拌情况下,固体废料比例与炉渣量之间的关系,缩短均匀熔化时间,电磁搅拌能够显著缩短高熔点合金元素的熔化时间。给出了采用电磁搅拌和气体搅拌对含硅铝合金熔化均匀所需时间的比较。这个炉子上同时装有多孔透气砖和电磁搅拌器,当采用电磁搅拌时,熔化均匀所需时间相对于气体搅拌能够缩短40%,取样位置位于合金加入位置的对面。采用气体搅拌时,气体离开透气砖后向上移动,形成局部对流,而横向传输以及对熔池的整体均匀相对于电磁搅拌大大降低。
即使气体搅拌相对于电磁搅拌也产生较多的氧化渣。气体在离开多孔透气砖后直接向上移动,在熔池表面达到最大速度,击破熔池表面,形成一个高湍流的‘渣眼’,增加了熔池表面与炉膛气氛的局部接触。观察到装料过程中固体废料的比例与炉渣量直接相关。随着固体废料比例的增加,氧化渣的数量也随之增加,能够在固体废料增加的情况下降低炉渣的产生。
()
电磁搅拌技术(Al-EMS)是一项已被证实和广为采用的对熔铝炉和静置炉中铝液进行有效搅拌的技术。目前已在全世界安装了150多台铝电磁搅拌器。能够缩短熔炼时间、增加产量、减少炉渣的形成、加快合金熔化和成分均匀、大幅度降低生产成本,设备投资回收期在很多情况下短于1年。铝熔池的有效搅拌能够增加冶金反应速度、改善传热和传质过程,是提高生产效率、改善铸造质量和降低操作成本的关键因素。电磁搅拌技术是对熔铝炉和静置炉中铝液进行搅拌的有效技术,并广为接受。通过改善传热和传质过程以及反应动力学,电磁搅拌技术能够缩短熔炼时间、减少炉渣形成,大幅降低操作成本。
电磁搅拌线圈是线圈为水冷式,安装于炉子底部或侧部,线圈与炉体之间没有直接的物理接触。可以采用通常的炉衬厚度,为了保证磁场进入熔池,必须在线圈前方的炉壳上安装奥氏体不锈钢窗。线圈采用低频行波磁场,磁场穿透炉壳和炉衬对熔池实现搅拌,其作用机理类似于线性电机。Al-EMS可以安装于新建炉子上,也可安装于改建炉子上,对于后者通常采用侧装式,圆形熔铝炉的侧装式系统包括一个或多个线圈、一个变频器、一个变压器、一个水冷站和控制系统,搅拌器可以采用本身的控制系统或连接于炉子控制系统进行操作,可以采用共用的电源和冷却水系统以尽量节省空间和降低成本。
电磁搅拌与人工搅拌和气体搅拌的比较,有14炉采用电磁搅拌和少量的气体搅拌,有16炉仅采用气体搅拌,采用电磁搅拌后,炉渣量由2.53%减少到2.15%,给出了圆形反射炉上的试验结果。有14炉采用电磁搅拌,17炉采用人工搅拌。试验过程中,废铝的加入比例从0到100%,其余为重熔铝锭,在使用电磁搅拌时平均废铝加入比例为80%,没有电磁搅拌时废铝比例为71%,在这种情况下,炉渣量从2.5%降到1.9%。采用人工搅拌时产生较多的炉渣主要有两个原因,一是在不进行搅拌时熔池表面温度过高,导致较高的氧化速率,另一个是在人工搅拌时熔池表面产生强烈的湍流,使大量铝熔滴卷入渣层内。
在有无电磁搅拌情况下,固体废料比例与炉渣量之间的关系,缩短均匀熔化时间,电磁搅拌能够显著缩短高熔点合金元素的熔化时间。给出了采用电磁搅拌和气体搅拌对含硅铝合金熔化均匀所需时间的比较。这个炉子上同时装有多孔透气砖和电磁搅拌器,当采用电磁搅拌时,熔化均匀所需时间相对于气体搅拌能够缩短40%,取样位置位于合金加入位置的对面。采用气体搅拌时,气体离开透气砖后向上移动,形成局部对流,而横向传输以及对熔池的整体均匀相对于电磁搅拌大大降低。
即使气体搅拌相对于电磁搅拌也产生较多的氧化渣。气体在离开多孔透气砖后直接向上移动,在熔池表面达到最大速度,击破熔池表面,形成一个高湍流的‘渣眼’,增加了熔池表面与炉膛气氛的局部接触。观察到装料过程中固体废料的比例与炉渣量直接相关。随着固体废料比例的增加,氧化渣的数量也随之增加,能够在固体废料增加的情况下降低炉渣的产生。
()